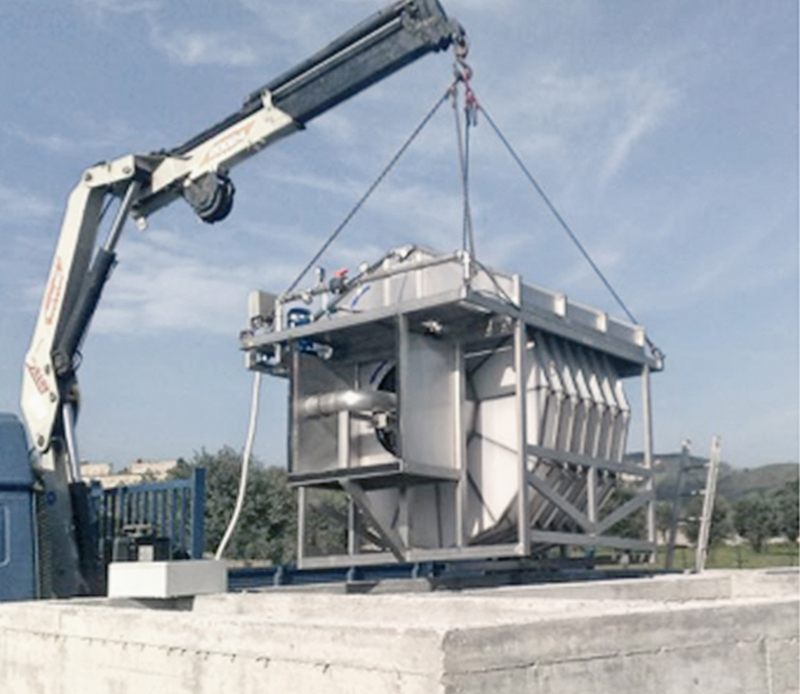
DESCRIPTION AND WORKING PRINCIPLES
Microfiltration technology combined with the polymer disc permits filtration spans of between 10 and 150 μm and quality separation even in the presence of high hydraulic pressure or peak loads of suspended solids. The new and fast nozzle cleaning system requires little energy and water. The fluids flow from the inside towards the outside, so the suspended solids are captured in the filter and the filter container remains perfectly clean. The modular nature of the disc filtering station is such that the filter units can be made extremely compact with filtering surfaces of up to 8 sq m for each sq m of occupied space.
The polymer fabric offers the following benefits over loose-fibre fabric: no suspended solids pass through the fabric during the washing phase; no suspended solids accumulate in the fabric, so cleaning is more efficient; virtually no wear and simpler maintenance. The incoming water is introduced, through the center tube, between the pairs of discs normally stationary, having a canvas of filtration able to retain suspended solids of magnitude greater than the spacing of the canvas used.
The water flows by gravity through the canvases installed on the discs and the solids are retained accumulating on the inner surface. Reached a certain level of clogging, permanently monitored by a sensor is activated by the rotation of the discs, providing for the discharge of accumulated solids through an opening between them. At the same time the system is activated in pressure washing, carried out in countercurrent, consists of a set of nozzles, easily removable to ensure perfect cleaning of filter cloths.
- Structure of the disc in stainless steel;
- Type of filter element: Polymer filter fabric or AISI 304/316;
- Tank for washing water;
- Backwashing system: mobile arrays of nozzles and multi-stage pump;
- Central shaft for supporting and feeding the filtering sections, made of stainless steel;
- Transmission system consisting of a chain made of special steel connected to a pinion;
- Control geared motor: with worm and helical gears;
- Cover with mobile windows for inspecting the filtering discs.
- Control board with IP55 protection.
APPLICATIONS
The uses of disc filters:
- Capturing residual suspended solids after secondary sedimentation tanks due to rising swollen mud, floating foam and/or excessive hydraulic pressure;
- Separation of excess mud after the submerged rollers, percolator filters and other biofilm processes, in lieu of conventional secondary sedimentation tanks;
- Reducing the content of phosphorous in fluids released by existing or new systems, possibly in combination with floccular-filtration;
- Separation of solid substances after chemicalphysical treatment of industrial sewage;
- Pre-filtration for: biofilm nitrification processes, for UV sterilization, processes with membranes, for surface waters to be converted into drinking water;
- Treatment of water for industrial use and for recycling;
- Increasing the performance of lagooning systems.