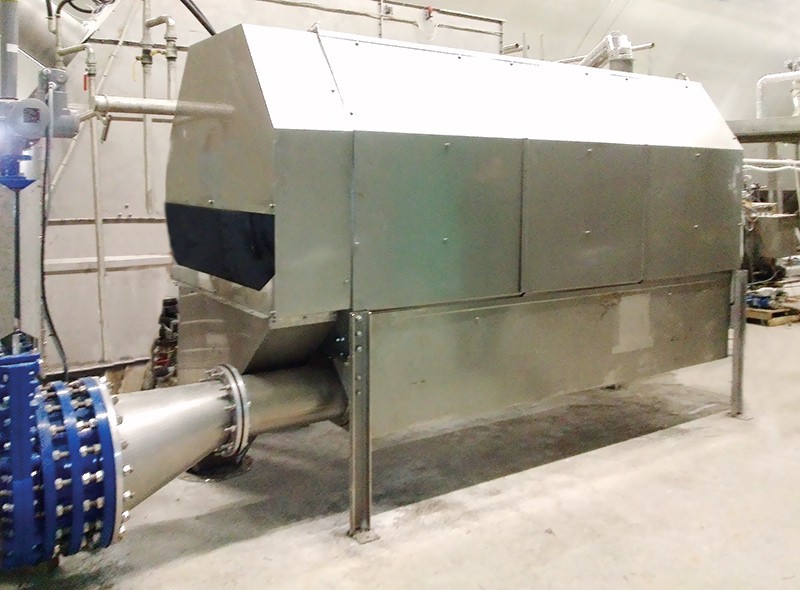
DESCRIPTION AND WORKING PRINCIPLES
X-INT.DRUM is an internally fed screening device with the flow being fed into the headbox and distributed onto the internal rotating surface of the screening cylinder. The screen has a solid, stainless steel unibody construction, a screening cylinder with interchangeable screening drum. A standard speed drive electric gear motor rotates the drum screening cylinder assembly at 8 rpm. The screening cylinder rotates quietly on four fully engineered wheels. Interchangeable drum screen, of stainless steel wedgewire mesh or perforated holes, from 0,25 to 6 mm provide the best screening/solids capture performance in all screening applications. The liquid in the headbox/distribution chamber is directed onto the internal rotating surface of the screen. Solids remain on the surface of the screen while the liquid goes through the screen media.
As the screen rotates, the solids roll on the face of the screening cylinder and are intercepted by the diverter flights. The diverter flights are mounted spirally, with the spiral pointing to the discharge end of the cylinder. As the screening cylinder rotates, the solids drop off one diverter flight to the next until they reach and drop off of the discharge end of the cylinder. The solids can drop off into a container; conveyor chute or sludge dewatering device for further processing to reduce the water content and/or increase the solids dryness. The unibody design of the X-INT.DRUM incorporates a drainage collection area including a flanged discharge pipe that directs the treated water to a tank, channel or pit, or on through further piping. The spraying/backwash system (inside or out) located on the upper half of the unit, will wash off any solids, grease or other materials sticking to the face of the screening media and thus keep the inside of the cylinder clean. The backwash can be set manually, timed, or programmed to operate on an as needed basis.