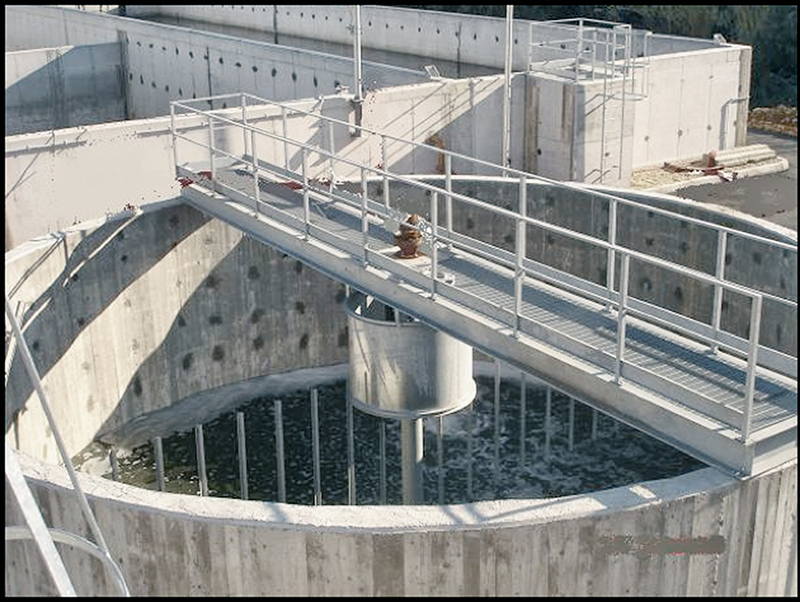
DESCRIPTION AND WORKING PRINCIPLES
The thickener bridge with central drive can be installed in different sizes of reinforced concrete tanks. Its purpose is to thicken and prepare sludge from the decanters for subsequent treatment. The in-flow of sludge is diverted by the settling cylinder to optimize thickening; special pegs turn very slowly to expel any air still in the sludge. Bottom scrapers remove the accumulated sludge for collection in the central hopper, where it is extracted through pipes. The clarified water flows in the peripheral channel.
MANUFACTURING FEATURES
- Torque shaft made of carbon steel suspended axially from the control unit.
- It is provided with fittings for the central distributor and for hinging the scraping unit;
- Double arm scraping unit made of carbon steel, on which are mounted the adjustable scraper blades and the thickener pegs;
- Replaceable scraper plates made of neoprene rubber.
- Cylindrical central baffle made of carbon steel;
- Peripheral spillway with Thompson profile made of stainless steel, with fixing and adjustment accessories;
- Direct control unit consisting of an electric motor and epicycloidal step-down gear, with alloy steel oil bath gears with cylindrical and helical teeth, and suitable protection for outdoor use;
- Central power supply at the top.