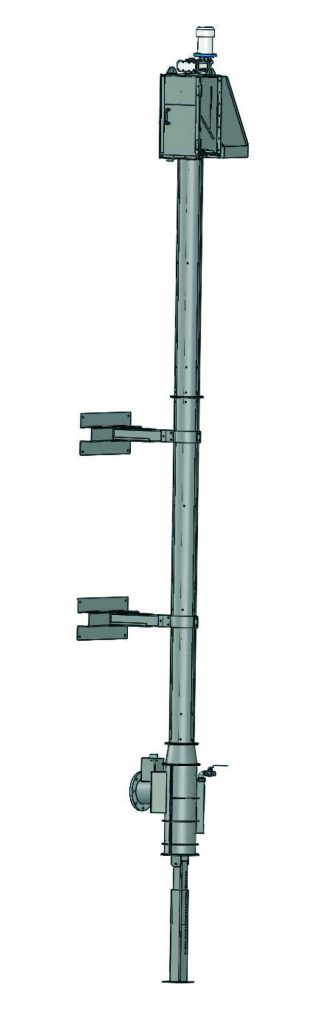
DESCRIPTION AND WORKING PRINCIPLES
The vertical screw screens are used to pre-treat any type of wastewater, whether municipal or industrial, but especially for the use in pumping stations, to protect the pumps. Depending on the type of application, is possible to choose between the version with or without compacting zone.
The main advantages of these models of machines are mainly the low cost of initial investment and the subsequent little maintenance required.
MANUFACTURING FEATURES
The construction of the machine can be made by choosing between the execution in Stainless Steel AISI 304 or AISI 316. The screw can be made of Stainless Steel (choosing between AISI 304 and AISI 316) or possibly also in carbon steel. The screw is always shaftless type.
The machine is constituted by a screen basket of Stainless Steel that may be “open-type”, that is directly installed in the channel or pit, or “closedtype” that can be coupled directly with the pipe from which comes the wastewater. The screen basket is cleaned by reinforced and bolted brushes, easily replaceable once worn out. These machines guarantee excellent performance even in the presence of fibrous or particularly long products, that do not cause clogging or blocks. In the standard model are always included the washings in the screening, in the transport and in the compacting area (when present), all controlled with a manual valve. The vertical screw screens, being them with or without copacting zone, lend themselves to a large variability of customizations, to make applications highly functional, according to the application.